汽車工業正經歷著一場以輕量化為核心的革命,而熱壓罐技術作為高性能復合材料制造的關鍵工藝,在這場革命中扮演著至關重要的角色。其獨特的優勢使得它能夠滿足汽車制造對輕量化、高強度、高安全性等方面的嚴苛要求,為汽車工業的發展注入新的活力。
一、熱壓罐技術助力汽車輕量化
傳統汽車制造主要采用鋼材,雖然強度高,但重量大,不利于提高燃油效率和降低排放。熱壓罐技術能夠制造出以碳纖維增強復合材料(CFRP)為代表的輕量化材料,其比重僅為鋼材的1/4,而強度卻可以達到鋼材的5倍以上。使用熱壓罐成型的CFRP部件可以顯著減輕汽車重量,從而實現:
提高燃油效率: 減輕車身重量可以降低發動機負荷,從而減少燃油消耗。
延長續航里程: 對于電動汽車而言,輕量化可以增加電池續航里程。
提升操控性能: 輕量化車身可以降低車輛重心,提高操控穩定性和靈活性。
降低排放: 減少燃油消耗意味著減少二氧化碳和其他有害氣體的排放,更加環保。
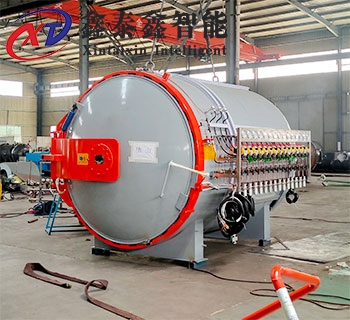
二、熱壓罐在汽車制造中的具體應用
熱壓罐技術制造的復合材料部件在汽車上的應用越來越廣泛,主要包括:
車身結構件: 車頂、車門、引擎蓋、行李箱蓋等,使用CFRP可以顯著減輕重量,同時提高車身剛度和抗沖擊性能。
底盤部件: 副車架、懸架臂、傳動軸等,使用CFRP可以降低簧下質量,提高操控性能和乘坐舒適性。
內飾件: 座椅骨架、儀表盤、門板等,使用CFRP可以實現輕量化和個性化設計。
其他部件: 電池殼體、保險杠、擾流板等,使用CFRP可以提升性能和美觀度。
三、熱壓罐技術的優勢
高性能: 高溫高壓環境有利于樹脂充分浸潤纖維,并實現完全固化,從而獲得高性能的復合材料制品。
復雜形狀: 熱壓罐成型工藝可以制造形狀復雜、尺寸精密的復合材料制品,滿足汽車設計的多樣化需求。
一致性好: 熱壓罐內溫度、壓力分布均勻,能夠保證制品性能的一致性,提高產品質量和可靠性。
生產效率高: 隨著熱壓罐技術的不斷發展,自動化程度不斷提高,生產效率顯著提升,成本逐漸降低。
四、挑戰與未來展望
盡管熱壓罐技術在汽車制造中展現出巨大潛力,但仍面臨一些挑戰:
成本較高: CFRP材料和熱壓罐成型工藝的成本相對較高,限制了其大規模應用。
回收利用: CFRP材料的回收利用技術尚不成熟,需要進一步研究和開發。
未來,隨著材料技術的進步、工藝的優化和成本的下降,熱壓罐技術在汽車制造中的應用將會更加廣泛。預計未來汽車將更多地采用復合材料結構,實現更輕、更強、更安全、更環保的目標。
總而言之,熱壓罐技術為汽車輕量化提供了一條有效的途徑,正在引領汽車制造行業的一場革命。隨著技術的不斷進步和應用的不斷深入,熱壓罐技術將為汽車工業的發展做出更大的貢獻,為人們帶來更加美好的出行體驗。